Release Notes
PlantPAx Process Library with Application Templates, Application Code Manager Library, Tools & Utilities, and Integration with E
Version 3.50.05 (released 1/2017)
Catalog Number Process Library
These release notes describe version information for Process Library, version 3.50.05 (released 1/2017).
Features
This release includes the following system features.
Logix CPU Utilization for Logix Version 24 and Later (L_CPU_24_up)
Feature First Identified as of PlantPAx Process Library Version 3.50.05
The L_CPU_24 (Logix CPU Utilization for Version 24 of Logix) instruction is replaced with a
new Add-On Instruction for Version 24 and Later: L_CPU_24_up. This instruction works
with Version 24 and Later (24, 26, 27, 28, 29 and 30) major firmware versions of the
CompactLogix 5370 and ControlLogix 5570 controllers:
- 1769-L16ER-BB1B
- 1769-L18ER-BB1B, 1769-L18ERM-BB1B
- 1769-L19ER-BB1B
- 1769-L24ER-QB1B,1769-L24ER-QBFC1B, 1769-L27ERM-QBFC1B
- 1769-L30ER, 1769-L30ERM, 1769-L30ER-NSE
- 1769-L33ER, 1769-L33ERM
- 1769-L36ERM
- 1756-L71, 1756-L72, 1756-L73, 1756-L74, 1756-L75
- 1769-L30ERMS
- 1769-L33ERMS
- 1769-L36ERMS
IMPORTANT: This instruction cannot get CPU utilization and other information from the
following controllers:
- 1789-L60 SoftLogix 5800 controller
- Emulate 5570 Studio 5000 Logix Emulate controller
- CompactLogix 5380 controllers (5069-L3xxEx)
- ControlLogix 5580 controllers (1756-L8xE)
To install this instruction in place of L_CPU_24 in existing version 24 applications, perform
the following steps:
- Open the existing application in Studio 5000 Logix Designer.
- Navigate to the existing L_CPU_24 instance in the application code. (A convenient
way to do this is to find the L_CPU_24 Add-On Instruction in the Controller
Organizer, then right-click and select “Cross Reference”. In the Cross Reference
dialog, double-click on the instance to go to that rung.)
- Select the existing L_CPU_24 rung, then right-click and select “Import Rung(s)”.
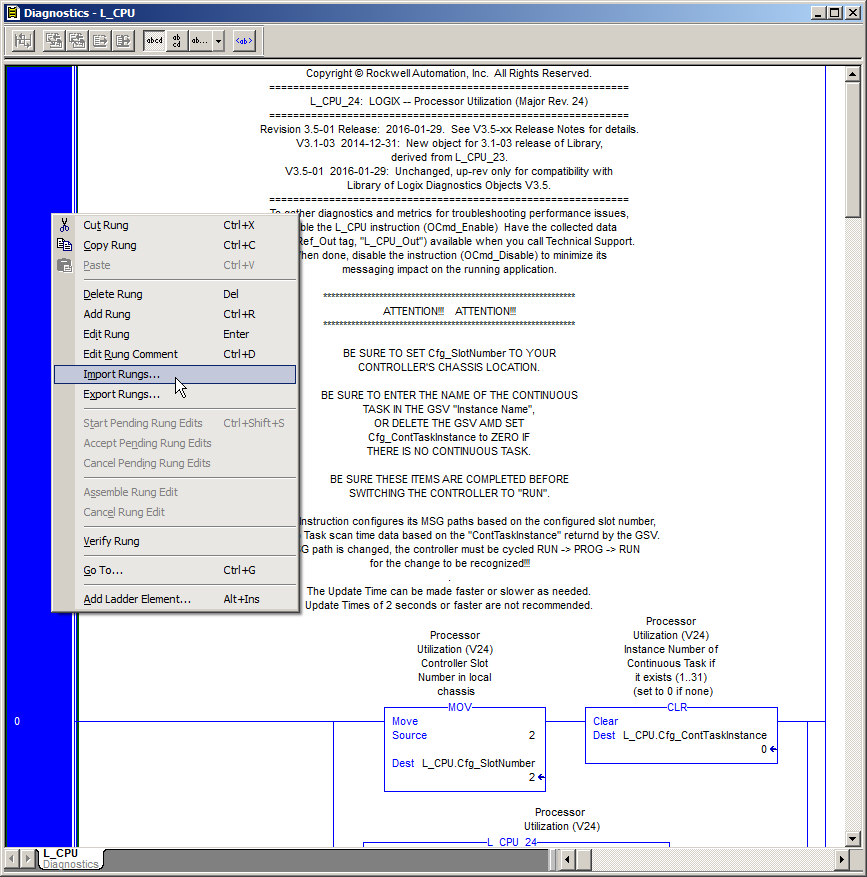
- Select the L_CPU_24_up_3_5-05_RUNG.L5X file from the Library download in
folder
- …\Files\Logix Diagnostic Objects Library\Logix Add-On Instructions.
- In the Import Configuration window, note the red flag next to the “Tags” item in the
tree. Select this item. In the first tag (L_CPU), change the Operation from “Use
Existing” to “Overwrite”. Click OK to begin the import.
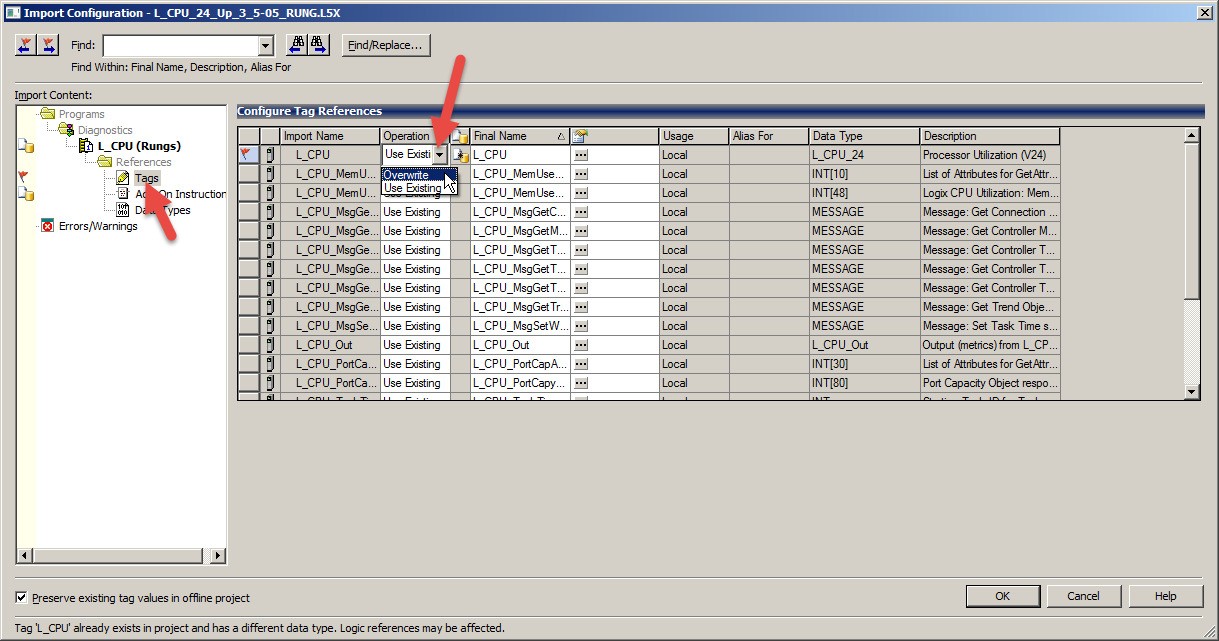
- The rung will be inserted AFTER the existing L_CPU_24 rung, and that rung will
have error marks (because the type of the L_CPU backing tag changed). Note (or
select and copy) the existing MOV and GSV (or CLR) instructions on the upper
branch.
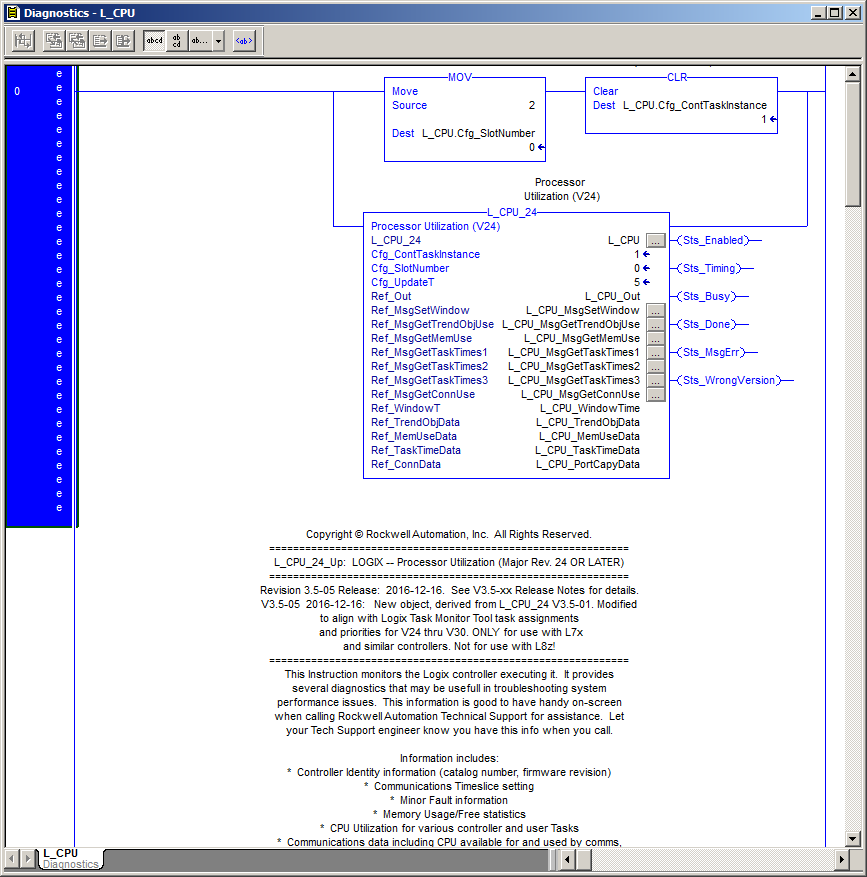
- Delete the old L_CPU_24 rung. In the new L_CPU_24_up rung, modify the upper
branch (paste if you copied) to restore the configuration of the Slot Number and
Continuous Task Instance.
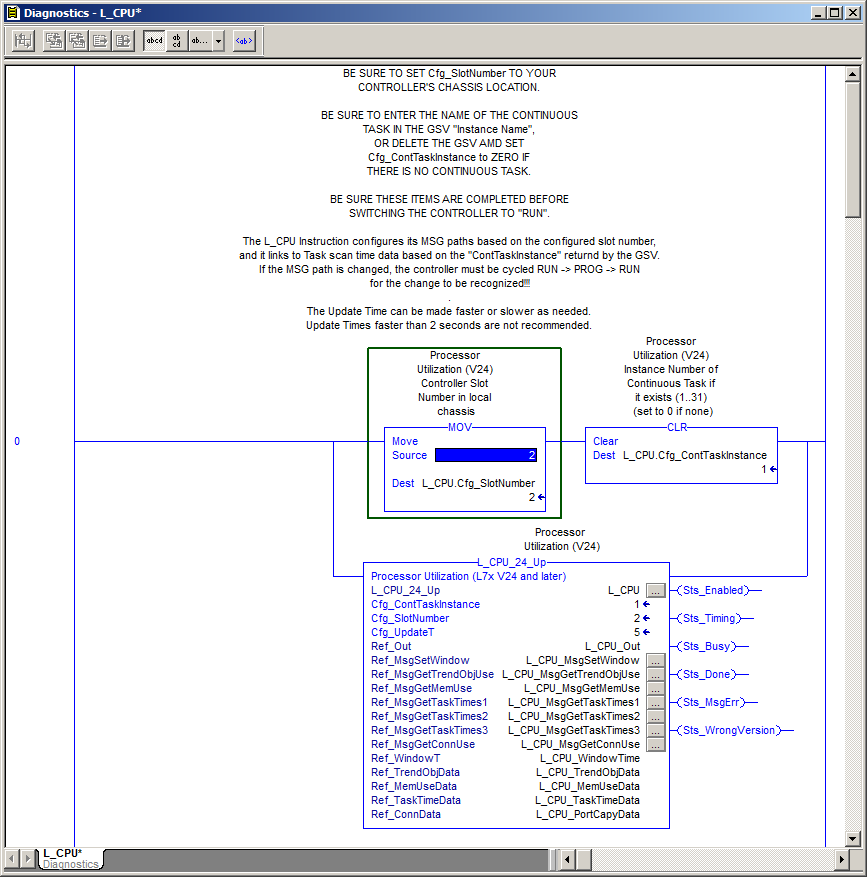
- Delete the (now unused) L_CPU_24 Add-On Instruction definition from the project.
- Verify and save the project and download to the controller.Only the Add-On
Instruction definition and the backing tag type are changed. The HMI components
and the other associated User-Defined Types (UDTs) and Tags are unchanged.
Alarm Builder Features (Version 5.5.5 of the Alarm Builder)
Feature First Identified as of PlantPAx Process Library Version 3.50.05
Updated ME Alarms XML Import File Builder Tool
Previous versions provided two methods for building the ME alarms XML import file: a
Quick Build that uses all Logix tags to build ME tags, and a “Long Method” where the user
selects the Logix tags to use.
The new version provides a single user interface for building the ME alarms XML import
file. Options are provided to use only tags from the Process Tree folders or to use all
controller tags. This single user interface is consistent with the AE alarm builder interface.
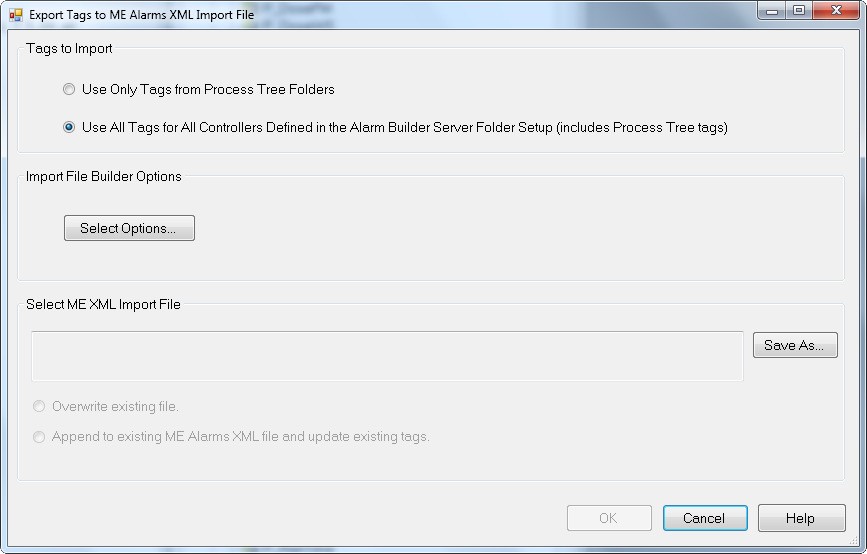
New ME Alarms XML File Builder Options
New options are provided to exclude alias tags and Input/Output program parameter tags
when building the ME XML file. These options are useful if alias tags are aliased to base
tags with the same data type – this prevents building multiple ME tags with the same alarm
triggers.
If the “Include Array Tag Elements” option is not selected, and alias tags are aliased to
array tag elements, then these new exclude options should not be used. These options
should also not be used if the alias tags are aliased to UDT elements and alarm definitions
are not configured for the UDT.Note InOut program parameters tags are now always
excluded from the export.
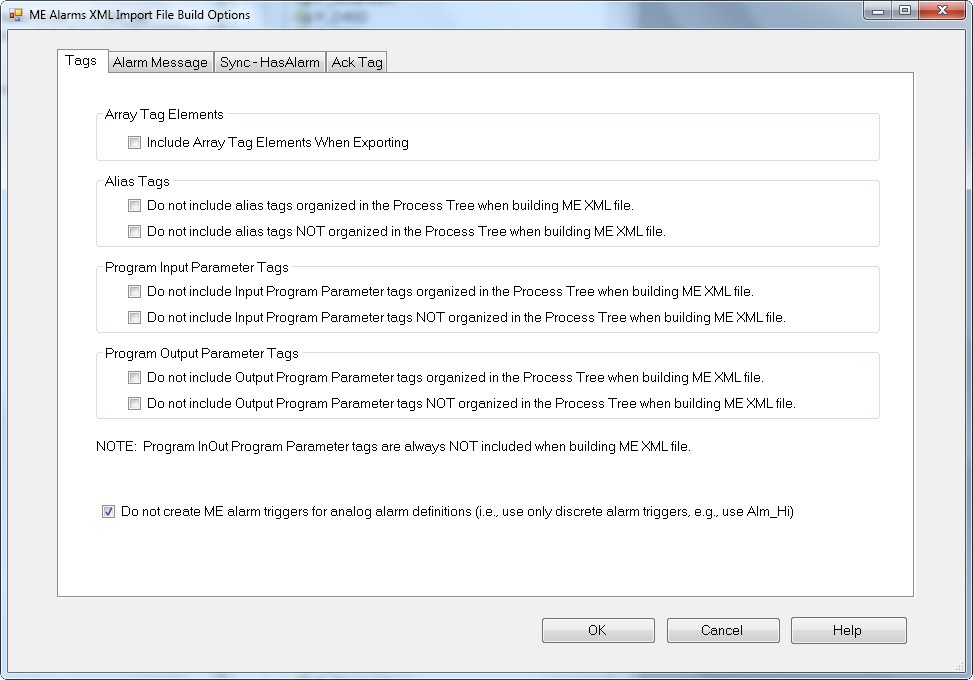
New options are provided for building the ME alarm messages:
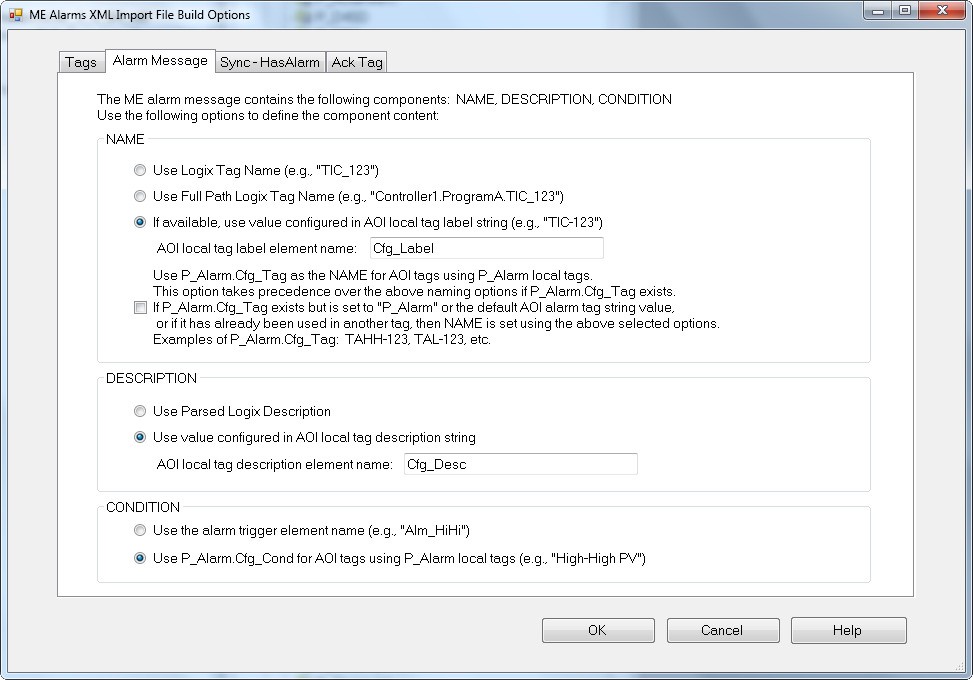
Process Library Migration Tool Features (Version 1.3 of the Migration Tool)
Feature First Identified as of PlantPAx Process Library Version 3.50.05
Execution Time Reduction
Coding changes made to reduce execution time for updating ACD files. The amount of
time reduction depends on the number of AOIs, IREFs and tag data changes. For some
test files, conversion time is reduced by about 40% compared to the last version.
Migration Tool Options
The ACD file migration tool uses Logix Services to import AOIs and other file changes.
Logix Services locks up when the importing AOIs for ACD files containing IREFs that are
linked to AOI tag parameters aliased to AOI local tags. So far, this problem has only been
found when converting Process Library AOIs version 3.0 and older. As a workaround, the
migration tool can check for these types of IREFs and replace them with blank references
before using Logix Services to import the new AOIs. After the AOIs are imported to the
ACD file, the IREFs are restored with their original references and the ACD file updated
again using Logix Services. For this version, options are added to allow the user to select
when to run the workaround method. In the previous version, the workaround was hidden
and always executed regardless of library version.
Startup Window Enhancements
New description added to the startup window to make clear which process library versions
are supported:
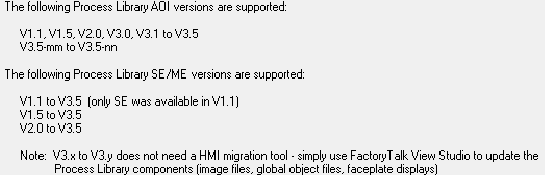
PowerFlex 6000 Medium Voltage Drive Support
Feature First Identified as of PlantPAx Process Library Version 3.50.05
A new Add-On Instruction, P_PF6000, and corresponding Faceplate were added to
support the PowerFlex 6000 Medium Voltage Variable Frequency Drive. Communication
is via an Anybus AB7007 EtherNet/IP - Modbus Serial gateway. The AB7007 profile is
supported in Logix version 20 and later software / firmware. The AOI and RUNG import
files are provided in Logix version20 format and work with version 20 or later. Operation
and setup are similar to the other PowerFlex drive Add-On Instructions, except that no
drive datalink setup is required (or available).
The P_PF6000 instruction is supported by the updated Process Library Online
Configuration Tool spreadsheet.
Along with addition of the new P_PF6000 Add-On Instruction, the following HMI displays
and global objects were added or modified:
- (RA-BAS) Process Diagnostics Objects.ggfx
- (RA-BAS) P_PF6000-Faceplate.gfx
- (RA-BAS) P_PF6000-Quick.gfx
- (RA-BAS-ME) Process Diagnostics Objects.ggfx
- (RA-BAS-ME) P_PF6000-Faceplate.gfx
- (RA-BAS-ME) P_PF6000-Quick.gfx
Because the 20-COMM-E (or similar) drive DPI communication adapter is not used, the
drive does not support using MSG instructions to read and write parameter values. All
data needed for this Add-On Instruction are contained in the Input and Output assemblies
and no MSG instructions are needed. The I/O assemblies do provide an interface to read
and write drive parameters from the controller, but this parameter read/write capability is
NOT part of the P_PF6000 Add-On Instruction.
Known Anomalies from Previous Releases
These anomalies are from previous releases but are still known in this release.
Corrected Anomaly with PlantPAx Process Library version 4.00.02
P_ValveSO Handling of Simultaneous Commands
Known Anomaly First Identified as of PlantPAx® Process Library version 1.00.00
When P_ValveSO receives simultaneous Open and Close commands, it alternates
between closing and opening, with the output toggling.
How Corrected: Logic was modified so that in the event of simultaneous commands, the
command for the de-energized (fail) state is the one accepted.
Corrected Anomaly with PlantPAx Process Library version 4.00.02
Read from Online Configuration Spreadsheet
Known Anomaly First Identified as of PlantPAx® Process Library version 3.00.00
Attempt to read configuration data from a controller fails with the following error
message:
Click OK for the following message:
By clicking OK, subsequent messages appear about location of cells which failed to read
and overall failure of the function.
However, the ‘Send To CLX’ function works properly, and once you do a successful
‘Send To CLX’, then the ‘Read From CLX’ function begins to work properly.
This only affects the Premier Integration Online Configuration Tool spreadsheet. The
Process Library Online Configuration Tool spreadsheet works correctly.
The spreadsheet’s Visual Basic for Applications (VBA) code associated with the Read
From CLX function was corrected to remove an improper VAR initialization.
Functional Changes
This release has the following functional changes from the previous release.
Lead/Lag/Standby Rank Value
Functional Change First Identified as of PlantPAx Process Library Version 3.50.05
The Lead / Lag / Standby Motor Group Add-On Instruction was modified to generate an
additional value, “Val_Rank”, which was added to the P_LLS_Motor User-Defined Type.
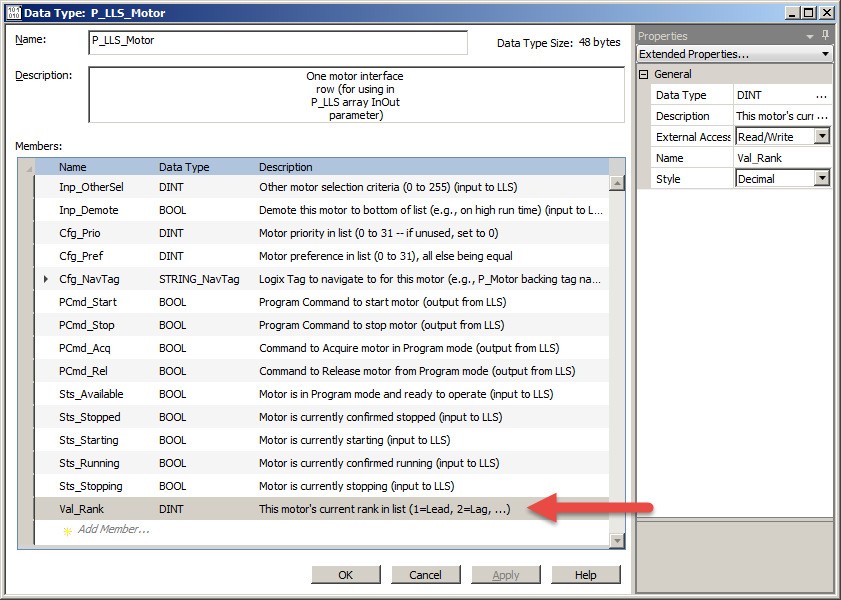
Logic was added to P_LLS so that each motor will now have its rank within the sorted
motor list made available for use in application logic. A value of 1 is given to the motor
assigned as Lead, a value of 2 to the first Lag, and so on, through the number of motors in
the group.
Notice that this Value is provided in the “Ref_Motors” array and not as a parameter on the
Add-On Instruction itself, and the array index is “zero-based”. So the rank of Motor 1 in the
P_LLS instance named “MyP_LLS” would be found at the address
“MyP_LLS_Motors[0].Val_Rank” (using the required naming convention for the motor
interface array tag).
Rockwell Automation recognizes that some of the terms that are currently used in our industry and in this publication are not in alignment with the movement toward inclusive language in technology. We are proactively collaborating with industry peers to find alternatives to such terms and making changes to our products and content. Please excuse the use of such terms in our content while we implement these changes.
Copyright © 2025 Rockwell Automation, Inc. All rights reserved.
Rockwell Automation, Allen-Bradley, and FactoryTalk are trademarks of Rockwell Automation, Inc.
To view a complete list of Rockwell Automation trademarks please
click here.Trademarks not belonging to Rockwell Automation are property of their respective companies.